Construction systems
Last updated: 9 August 2023
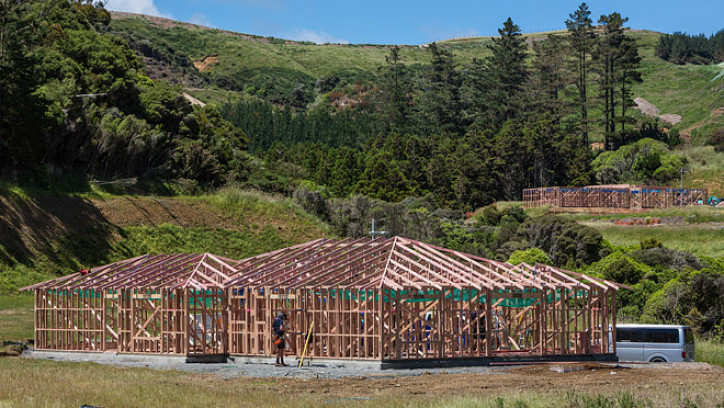
Which construction system is best for your design, location and climate?
Construction systems
The term 'construction system' refers to the way a home is built – that is, the materials and methods used to construct its foundations, floor, walls, and roof.
There are a number of different construction systems which are typically put into three categories – lightweight, such as timber or light steel-framed construction systems, medium weight, such as solid timber, and heavy weight or high mass, such as concrete block. Each has its benefits and constraints. Features of your site, such as ground conditions or steep slopes may affect your choices – your designer will be able to talk you through these.
Lightweight/low mass walls
Lightweight construction systems typically have walls consisting of either timber or steel framing with cavities between the outer cladding and the inner lining. These cavities are usually filled with the insulation material. But there are also other less common lightweight systems.
Lightweight walls are suitable for a large range of cladding options. Most lightweight walls will require a drainage cavity between the framing and the cladding to allow any water that penetrates the cladding to run back out rather than be absorbed into the framing.
Certain ground conditions may make lightweight construction desirable if it avoids the need for extensive earthworks and/or special foundations.
Another advantage of lightweight wall systems is that wall construction can be faster than for heavy mass walls. Many of the wall systems are at least partly pre-assembled off-site meaning that they can be precision fabricated in a factory. Typically this is just the wall and roof framing, however in some cases walls are clad, or even installed with services and insulation and linings in the factory. This lets the building be closed in faster, meaning that construction progress is less weather dependent.
Lightweight materials generally have a lower amount of embodied carbon than heavyweight construction at completion. However, a well-insulated and designed heavy mass building may be as or even more environmentally friendly than a poorly insulated or designed lightweight building over its lifetime.
Lightweight walls tend to be less insulating to sound than solid heavy-mass walls.
Framed
Framed wall constructions are the most common light-weight systems. They consist of timber or steel frames with cavities in-between. Insulation is placed between the studs, and in some systems can also be placed as a complete layer over the outside of the framing.
Steel is a very good thermal conductor, so it is generally necessary to apply strips or sheets of insulation as 'thermal breaks' between the cladding and the framing. This reduces the flow of heat from inside to out, and keeps the framing warmer, reducing the likelihood of condensation occurring where framing meets the internal linings.
Timber construction and steel frame construction have more information.
Structural insulated panels
Structural Insulated Panels (SIPs) consist of insulation material (typically plastic foam insulation), which is sandwiched between sheets of structural board such as plywood, oriented strand board (OSB) or metal.
Many SIPs systems are used for walls, and can also be used for roofs and floors.
SIPS walls tend to have higher insulation values than framed constructions due to the almost continuous layer of insulation. However, if the surfaces and end sections are made of steel rather than timber this creates thermal bridges which reduce the overall thermal performance of the system.
SIPs walls consist of large panels with engineered connections between the panels. The walls are more airtight than framed walls, in particular framed walls with strip cladding such as weather boards.
Strawbale
Straw bale walls can be built quickly and easily. Dry bales of straw are stacked like bricks to form a wall. They are tightly wired together and then plastered. The plaster must allow the bales to breathe in order to prevent moisture build-up which causes rotting. The finished wall can look like a stucco or adobe wall.
If driving rain is a feature of the local climate, some sort of extra waterproof protection is needed ‑ or straw bales may not be the best construction option.
To avoid pitfalls it is essential to have the project designed, supervised and built by people who have the experience with straw bale buildings. There is no New Zealand Standard for construction with straw bale, so it may be more difficult to demonstrate compliance with the Building Code.
Other types of construction has more information.
Cladding
Lightweight walls can have a large variety of claddings including
- Sheet cladding such as plywood or fibre-cement
- Weatherboards made from timber, PVC, aluminium, fibre-cement or other materials
- Clay or concrete brick veneer
- Autoclave aerated concrete (AAC) panels
The cladding will usually have to be separated from the framing by a drainage cavity.
Lightweight cladding materials such as sheets and weatherboards will require less bracing to resist earthquake damage than heavier materials, such as brick veneer.
Flooring options
Because the weight of the walls is comparatively low, these wall constructions can either be used with a concrete slab or with a suspended concrete or timber floor.
Medium weight/medium mass walls
Medium-weight wall properties, advantages and limitations are usually similar to lightweight walls.
Medium mass walls are usually solid walls consisting of a material that is comparatively light. A typical medium mass wall type is a solid timber wall.
Heavyweight/high mass walls
Heavyweight walls typically consist of concrete blocks or precast concrete. If designed and insulated properly the thermal mass in the concrete can be utilised to store heat from the sun, reducing heating and cooling energy and improving comfort.
Using thermal mass for heating and cooling has more information.
Heavy mass walls have very good sound insulating characteristics and may therefore be a good option for noisy environments.
If the building has multiple storeys or complex shapes concrete is often used at least in some of the load bearing walls.
Homes with heavy mass walls typically have a slab-on-ground floor. On a sloping site, this may require expensive foundations. Specific engineering design will be required for sites with certain ground conditions, such as those prone to liquefaction.
Concrete block
Concrete is familiar to the majority of building professionals. It is usually plastered on the outside and strapped and lined internally, but it is possible to also use other cladding systems.
Concrete is durable, fire resistant, vermin and insect proof and a good sound insulator. Soft furnishings and textiles (such as carpets and curtains) will help reduce the amount of echo from sound bouncing off the hard surfaces. Ask your designer about incorporating acoustic insulation, especially in large spaces with little furniture, carpets or curtains.
Concrete construction has more information.
Concrete tilt-slab and concrete sandwich panel
Concrete tilt slabs have similar properties, advantages and limitations as concrete blocks. Their main advantage is their large format, which means that construction time can be reduced compared to concrete blocks. In order to meet thermal performance requirements, they are typically insulated and rendered (plastered) on the outside, or strapped and lined on the inside with insulation in the cavity. External insulation allows the concrete (which may be plastered) to be exposed on the inside, contributing to the thermal mass.
Concrete construction has more information.
Concrete sandwich panels consist of two precast slabs with a layer of insulation, usually plastic foam insulation, sandwiched in between. They have the advantage of being able to be rapidly set up on site.
Because of the built-in insulation they tend to have good insulation properties. If the concrete is left exposed on the inside it can contribute to the thermal mass of the building.
Insulated concrete formwork
Insulated concrete formwork (ICF) consists of a system where hollow expanded-polystyrene blocks are fitted together like building blocks. Reinforcing is inserted and concrete is poured into the voids. The polystyrene formwork is left in place and will typically provide enough insulation to meet or exceed Building Code requirements without any additional insulation.
ICF must be properly clad to keep water out. In most cases both sides of the wall are plastered or lined to protect the polystyrene and improve appearance.
As well as the strength and durability of concrete, ICF has:
- integrated insulation
- draught-proofing
- good sound insulation.
Concrete construction has more information.
Rammed earth
Rammed earth walls are formed from damp soil that is tamped between shutters with manual or pneumatic rammers. Often cement or hydrated lime is added to improve durability. The walls are often left as they are and can reveal a natural-looking pattern from the ramming process.
Rammed earth walls have most of the advantages and limitations of other heavy mass walls. However, rammed earth walls are limited to the shapes that can be built with removable shuttering.
Rammed earth walls do not usually have an insulation layer added, and their inherent thermal performance is limited.
Consistent workmanship is particularly critical for both the appearance and the strength of rammed earth walls, so site work has to be of high quality. NZS 4298 – Materials and workmanship for earth buildings – outlines workmanship requirement including compression and durability tests, and a simple on-site test for moisture content.
There are a number of related earth building methods.
Other types of construction has more information.
Flooring options
On level sites concrete slabs on the ground are cheaper than timber floors, and are now standard practice in many homes. A layer of insulation under the slab and around the perimeter provides a significant boost to the thermal performance of the slab. An insulated slab is particularly important for homes where the thermal mass is used as a feature of passive solar design.
TIP - Thermal mass for heating and cooling
Don't get thermal mass of a building confused with the weight of just the walls or floor. A building with lightweight timber walls but an exposed concrete slab floor will have more useful thermal mass than a house with concrete walls that are insulated on the inside and a heavy carpet on a slab floor.
For thermal mass the critical question is whether the mass is exposed to solar gain or another radiant heat source inside the house.
Using thermal mass for heating and cooling has more information.
Roofing options
The wall construction type generally does not limit the roof type you can use. For example it is possible to have a concrete tile roof on a lightweight timber framed wall.
The type of roofing (metal sheets, butyl on plywood, concrete tiles, etc) typically has little effect on the thermal performance of the house.
The choice mostly comes down to personal preference and aesthetics, alongside maintenance requirements and expected lifespan.
Some roof types such as concrete tiles have higher upfront costs than others such as corrugated iron, but are more durable and require less maintenance in the long run.