Concrete construction
Last updated: 9 August 2023
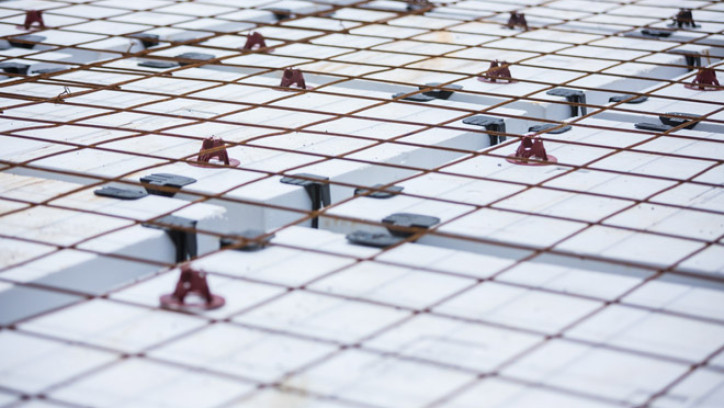
Concrete is strong, durable, fire-resistant and good at storing heat. It's also a relatively economical and well understood building material.
Concrete used for construction
Concrete has been used in construction around the world for over one thousand years. Romans used concrete for many of their buildings and monuments, some of which are still around today.
It is a familiar building material for many building professionals. Common forms of concrete construction include concrete blocks, concrete poured into formwork and allowed to set, and precast concrete panels.
Made from Portland cement mixed with sand and gravel (aggregates) and water, concrete is a hard, dense material. Cement is made by heating limestone and clay, then grinding it with gypsum. The powder, when mixed with water undergoes a chemical reaction and cures into a hard solid. The ratio of each ingredient is carefully measured to maximise the strength and durability of the final product.
Concrete is good in compression, and as a result is primarily used for load-bearing applications, such as exterior walls. Concrete is weak in tension, so steel reinforcing is used to add strength and reduce the likelihood of damage in a seismic event. Concrete floors have a layer of mesh added near the surface to reduce the likelihood and severity of cracking as the slab cures and dries.
While relatively cheap, concrete is heavy and has specific transportation requirements. On level building platforms, concrete slab floors are typically more cost-effective than suspended timber floors. Suspended concrete floors can be used on sloping sites.
Concrete is porous and floor slabs need a damp proof membrane underneath them to prevent water being absorbed from the ground. Concrete and concrete masonry walls generally need finishes such as paint on exterior surfaces.
Concrete is also low maintenance, durable, immune from attack by insect and vermin, and long lasting. However, the invasive root systems of some climbers such as ivy can damage concrete if allowed to take hold.
Because concrete doesn't sustain a flame, it is often used for fire separations between dwellings, or as boundary walls.
Is it compatible with passive design?
Concrete is good at absorbing and retaining heat during the day, and radiating it out at night when temperatures fall. On summer days, it can absorb heat from the surrounding air and keeps your home cooler.
While concrete is a good material to use for thermal mass, it is not a good insulator. To keep stored heat from escaping into the colder surrounding ground, a concrete slab floor should be insulated both underneath and around the edges of the slab. Exterior concrete walls should be insulated on the exterior if they are used for thermal mass, or on the interior if they're not.
If you're using concrete as heat storage, don't cover it with carpet where the sun shines on it – this stops the slab from warming up. However, not having a floor covering can also make the concrete floor less forgiving if you trip or fall. Consider partially covering the slab, for example with exposed concrete or tiles around the perimeter and carpet or mats in the centre.
Using thermal mass for heating and cooling has more information.
With concrete construction, think about the placement of doors and windows at the start – retrofitting openings later can be difficult and expensive.
Concrete is a good sound insulator. However, without soft surfaces such as carpet and curtains, sounds inside your home may echo and impact noise may transfer through the floor to any space under the floor.
TIP - Using concrete for thermal mass
A concrete slab floor exposed to direct sunlight is one of the most effective ways to absorb and store warmth in your home. Properly designed with maximum exposure to winter sun over the middle of the day, the slab will absorb energy from the sun during the day and then radiate that warmth out as the temperature drops in the evenings.
Environmental considerations
Curing concrete produces large amounts of carbon dioxide as part of the chemical reaction process.
At the end of life, concrete can be crushed and recycled into aggregate, and the reinforcing can be removed and recycled.
Types of concrete construction
Concrete slabs
Concrete slab floors are now the most common type of ground floor in New Zealand homes.
Curing concrete slabs
All fresh concrete slabs should be cured slowly for the first week to reduce the number and severity of cracks. This is done by using a fine water spray, laying a polythene sheet or wet hessian over the top, or using a chemical curing compound. If water is used, sand can be piled up around the edges of the slab to retain a wet surface layer. Even when cured slowly, some minor cracking of concrete can be expected.
If the concrete slab is to have an exposed aggregate or polished finish this must be specified before the concrete is laid. Different aggregates are used to provide a different look, and in some cases dye can be added to tint the mixture. Talk to your designer about your options.
Reinforcing
All concrete floor slabs are designed to meet Building Code requirements for structural performance. They are typically required to have reinforcing steel mesh, and have perimeter foundations tied to the concrete slab with reinforcing steel. You can’t use unreinforced slabs anywhere in New Zealand unless it is a specific engineering design and approved by the council.
The purpose of the mesh is to stop or limit the spread of a crack if it opens up, and to limit differential settlement across a crack. Without mesh, a crack in an unreinforced slab is likely to widen and spread across the whole slab. Tying the perimeter foundation to the slab reinforcement will limit movement and damage from earthquake shaking. Large slabs are designed to have some movement joints.
Heating systems
Slabs can have water pipes or electrical cables embedded in them for heating and cooling. If anything goes wrong with these embedded systems they are very hard to fix. With embedded heating systems, having thick, continuous insulation underneath and around the sides of the slab is particularly important.
Insulation
A concrete slab will benefit from having a continuous layer of insulation underneath and around the sides of the slab.
Pod-style concrete flooring incorporates polystyrene or hollow plastic pods beneath the slab. This both reduces the amount of concrete required, and increases strength across the slab by creating a web of beams to strengthen the slab into a ‘raft’. This type of system is often used in areas with variable soil conditions. Ask your designer if the system has insulation extending between the pods and up the edges of the slab as well. Without a complete layer of insulation, in most cases the performance of pod-style floors is only marginally better than plain slab-on-ground in terms of thermal performance.
Suspended floors
Suspended concrete floors can be used for domestic applications. These are often either precast flooring panels or a composite system consisting of concrete poured onto a metal tray system. These systems can add thermal mass on upper levels, but require good insulation where they back onto unconditioned spaces (eg a garage) and subfloors.
Concrete blocks
Walls can be made from hollow concrete blocks that are laid like bricks, reinforced with steel bars during construction, and filled with concrete. These blocks are also called concrete masonry units (CMUs).
It is preferable to design buildings to fit standard block sizes to avoid cutting blocks to size. Block laying must be done by a skilled block layer who is a licensed building practitioner.
The LBP website has more information about when you need to use a licensed building practitioner
Sites with restricted or poor access may make delivery of pallet loads of blocks difficult and/or costly. This is because pallet loads of blocks are heavy, and are likely to need trucks with cranes, or forklifts to move them.
Standard concrete blocks don't have enough insulation on their own to meet the minimum thermal performance requirements of the New Zealand Building Code. Insulation can be added to the outside or inside of the wall.
Precast concrete
Precast concrete panels are commonly used in commercial buildings, and can also be used in residential buildings. These can be poured on-site (tilt-slab) or precast off-site and lifted into place.
There are two types of panels – solid, and sandwich. Solid concrete panels will typically need insulation, either on the inside or outside, to meet or exceed the thermal performance requirements of the Building Code. Sandwich panels have a layer of insulation foam between the two concrete faces, which provides an almost continuous layer of insulation and allows the inside face to be used as thermal mass.
Poured concrete
Another option for solid concrete homes is for concrete poured on-site. The concrete is poured into formwork that contains the pre-prepared reinforcing steel. Formwork is typically made of plywood or boards, and can be textured or incorporate patterns to provide visual interest to the face when the formwork is removed.
The formwork and reinforcing takes time to put in place, but the process of pouring is relatively fast. The concrete cures inside the formwork for several days until it is strong enough for the formwork to be removed. The concrete will continue curing over a number of months until it reaches maximum strength. Ventilation over this time is very important to remove the continuing release of moisture and prevent indoor moisture issues.
Like solid concrete panels, poured concrete walls will typically require insulation on the inside or outside in order to meet or exceed the thermal performance requirements of the Building Code.
Insulated concrete formwork
Insulated concrete formwork provides permanent formwork that concrete is poured into. It is made up of two polystyrene faces joined together by webs at regular intervals, and is fast to put together. The prepared reinforcing steel is contained within the void in the middle.
Once poured, the polystyrene is left in place on both sides, so removes the potential benefit of thermal mass exposed to the inside. The finished faces are typically rendered on the outside, and lined on the inside.